Таблица 5.2
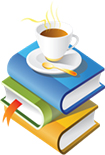
в связи с округлением. По данным, приведенным в табл. 5.3, строится диаграмма Парето, содержащая:
• горизонтальную ось, на которой в том же порядке, что и в табл. 5.3, нанесены наименования агрегатов;
• левую вертикальную ось, на которой в соответствующем масштабе отложено суммарное число дефектов (максимальное значение отрезка левой вертикальной оси равно N);
• правую вертикальную ось, на которой в соответствующем масштабе отложены значения накопленного процента дефектов (максимальное значение отрезка правой вертикальной оси равно 100 %).
Максимальные значения левой и правой вертикальных осей, очевидно, равны между собой. В построенных осях диаграммы откладывают число дефектов агрегатов в соответствующем масштабе в виде «столбиков» и накопленный процент дефектов.
Пример диаграммы Парето для данных табл. 5.3 приведен на рис. 5.3. Из анализа диаграммы следует, что около 70 % дефектов приходится на 3 системы автомобиля: электрооборудование, трансмиссия, кузов. Таким образом, для эксперта-аудитора эта диаграмма Парето дает информацию о правильности подбора стендов, размещении участков диагностирования и тех «узких» местах производства, которые должны быть охвачены системой качества.

Рис. 5.3
Следует отметить, что диаграмма Парето для отдела качества ремонтного предприятия является информацией о первоочередных мероприятиях по управлению (повышению) качества ремонта автомобиля. Для данного примера система мероприятий должна строиться таким образом, чтобы в нее были включены 3 выделенных агрегата автомобиля.
Диаграммы Парето целесообразно строить по нескольким признакам, тогда они несут много разнородной информации, что важно для всесторонней оценки системы качества при аудите:
1) потери (затраты) времени, труда, средств;
2) себестоимость продукции (ремонта);
3) персонал;
4) безопасность;
5) технологические операции;
6) несоответствия;
7) участки предприятия;
8) сырье и т. п.
Рассмотрим еще один пример, демонстрирующий эффективность анализа качества с использованием диаграммы Парето.
Исследуется качество работы двух ремонтных участков, каждый из которых обслуживает по два ремонтных и диагностических стенда. Качество работы участков оценивают по числу дефектов трех типов (Д1, Д2, Д3), выявленных за 4 месяца работы.
Результаты наблюдений представлены в табл. 5.4.
Таблица 5.4

Примечание. Запись АДi– (i = 1, 2, 3) означает, что зафиксировано А дефектов типа Д;.
Из анализа табл. 5.4 следует, что:
• если построить диаграмму Парето по участкам, то можно сделать вывод о том, что качество работы участка В хуже, чем участка А;
• если построить диаграмму Парето по стендам, то можно сделать вывод о том, что качество работы стенда 3 хуже, чем остальных стендов. Следовательно, проблема качества связана не с участком В, а со стендом 3;
• если построить диаграмму Парето по видам дефектов, то можно сделать вывод, что дефект Д1 встречается наиболее часто. Таким образом, второй аспект повышения качества обусловлен снижением числа дефектов Д1. Этот вывод устойчив и не зависит от вида стенда;
• если построить диаграмму по месяцам работы, то можно сделать вывод, что наиболее неблагополучным в аспекте качества является третий месяц. Эта информация подлежит дальнейшему анализу для устранения причин дефектов.
В некоторых случаях целесообразно строить совместно диаграмму Парето и схему «причины – результаты» для выделения «узких» мест системы качества, формирования плана проверок и ранжирования факторов, влияющих на качество.
В заключение этого раздела следует остановиться на идее визуализации (наглядности) анализа качества. Сравнивая табл. 5.3 и рис. 5.3, можно сказать, что каждая из этих форм содержит одну и ту же информацию о качестве. Однако, глядя на табл. 5.3 (которая содержит данные только по семи агрегатам), можно сказать, что «глаза разбегаются» от обилия цифр. В отличие от этого, диаграмма Парето (рис. 5.3) сразу показывает наиболее «дефектонос-ные» агрегаты, что, в свою очередь, дает импульс специалистам для дальнейшего анализа.
5.3.3. Применение простейшего корреляционного анализа для сертификации систем качества
Цель применения простейшего корреляционного анализа – определить и оценить линейную связь между фактором и показателем качества. При этом предполагается, что:
• связь между показателем качества и фактором случайная;
• значения показателя качества и фактора, который, возможно, влияет на него, имеют нормальное распределение вероятностей.
Типичные варианты исследования связи:
• показатель качества ремонта – себестоимость ремонта;
• затраты на ремонт – доремонтный ресурс;
• затраты на ремонт – квалификация рабочих;
• ресурс между ремонтами – год выпуска изделия;
• затраты на диагностическое оборудование – показатель качества ремонта.
Обнаружение связи или доказательство ее отсутствия между фактором X и показателем качества Y дает возможность объективно оценить проверку элементов системы качества. Например, если связь между показателем качества ремонта и квалификацией рабочих не обнаруживается, то это говорит о том, что проверка персонала этого объекта может быть ослаблена.
Для предприятия, внедряющего систему качества, использование методов корреляционного анализа дает возможность осознанно (на основе данных, а не инженерной интуиции) реали-зовывать мероприятия по управлению качеством продукции.
Например, исследование связи между метрологической характеристикой стенда для диагностирования тормозных качеств X и процентом возврата автомобилей после ремонта (по причине низкого качества тормозной системы) Y показало, что нецелесообразно управлять качеством ремонта тормозной системы за счет улучшения характеристик диагностического стенда.
Визуализацию корреляционного анализа осуществляют с использованием диаграмм рассеяния.
Порядок построения диаграммы рассеяния:
1) определяют показатель качества Y, подлежащий анализу, и параметр X, влияющий на этот показатель;
2) уточняют инженерные аспекты этой связи, т. е. физическую возможность зависимости Y (показателя качества) от параметра X;
3) определяют период наблюдений, на котором собирают данные о значениях X и соответствующих значениях Y. Таким образом, формируются два массива данных: Х
4) строят координатную сетку: по горизонтали – ось, на которой откладывают в соответствующем масштабе значения X; по вертикали – значения Y.